Six Sigma methodology emphasizes the importance of obtaining and implementing the voice of the customer (VOC) in the quality improvement process. Quality and value can be defined only by the customer. Therefore, an organization that sees itself through its customer’s eyes and evaluates itself the way the customer does has an important advantage in its pursuit of improving quality.
In the traditional approach to developing a product or service, little or no effort is made to capture the VOC and even less effort is made in planning a product to meet the customer’s needs. This method is inefficient and out of touch with customer needs and usually requires extensive redesign to work out conflicts in the process.
In contrast, a product development process that is based on VOC data and developed around the needs expressed by the customer is far more efficient and effective. The planning phase requires more time to integrate VOC information, with the idea that the product or service is delivered to the customer faster and does a better job of meeting customer needs.
Quality Function Deployment
The Six Sigma methodology calls the process of transforming VOC data to design requirements and performance targets Quality Function Deployment (QFD). In keeping with the rigorous nature of the Six Sigma process, QFD uses matrices to ensure that customer requirements are visually displayed and that they are satisfied by one or more design elements.
House of Quality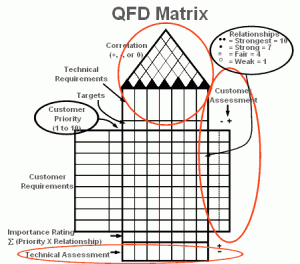
The matrix used to connect customer requirements to internal process and product requirements is called the House of Quality, it contains:
- the features customers want in the order of importance
- the capabilities the company can use to meet customer requirements
- the correlation that company capabilities have with one another
- a comparison of the organization’s and the competition’s ability to meet customer requirements
This House of Quality matrix is the tool for converting customer needs into design requirements. This tool is used to convert customer requirements into process outputs for all four stages of the Quality Function Deployment process, including:
Design requirements stage – A product planning matrix helps match customer needs with design options, this ensures that each design requirement is filled by one or more design elements.
Part characteristics stage – A part deployment matrix helps determine how the finished part will satisfy customer needs.
Process requirements stage – A process planning matrix is used to determine how customer requirements can be turned into process requirements that will help decide the process methods.
Production operations stage – The production planning matrix turns customer requirements into the specific steps of the production operation.
Employing the QFD process and House of Quality matrices to each stage of product and service development process not only helps ensure that the final product or service meets the needs of customers, it can also help to identify waste. Company capabilities that have no corresponding customer requirements are considered non-value-added activities and can be eliminated.